Working as an electrical technician in a facilities management (FM) company is a challenging and rewarding career. Electrical technicians are crucial for ensuring the safe and efficient operation of electrical systems within buildings, factories, and various other facilities. Therefore, the interview process for such roles can be rigorous, requiring both technical knowledge and an understanding of facility management principles.
we will cover the top interview questions you might face when applying for an electrical technician role in an FM company. We’ll also provide detailed explanations, possible answers, and tips for success.
Table of Contents
1. Introduction to Electrical Technician Roles in FM Companies
- Job Description: Electrical technicians in FM companies are responsible for installing, maintaining, and repairing electrical systems. This includes everything from wiring and circuits to transformers and generators. Their role ensures the smooth operation of electrical components in commercial, industrial, and residential facilities.
- Skills Required:
- Strong technical knowledge in electrical systems and regulations.
- Problem-solving abilities.
- Communication skills to liaise with other team members and clients.
- Hands-on experience with tools, testing equipment, and safety procedures.
2. Common Technical Interview Questions
Question 1: Can you explain the principles of three-phase power
- Explanation: Three-phase power is a common method of alternating current (AC) electric power generation, transmission, and distribution. It is a type of polyphase system and is the most common method used by electrical grids worldwide to transfer power.
- How to Answer: When answering this question, emphasize your understanding of how three-phase power works. Discuss the differences between single-phase and three-phase systems, and explain the benefits of using three-phase power in facilities management, such as increased efficiency and reduced energy loss.
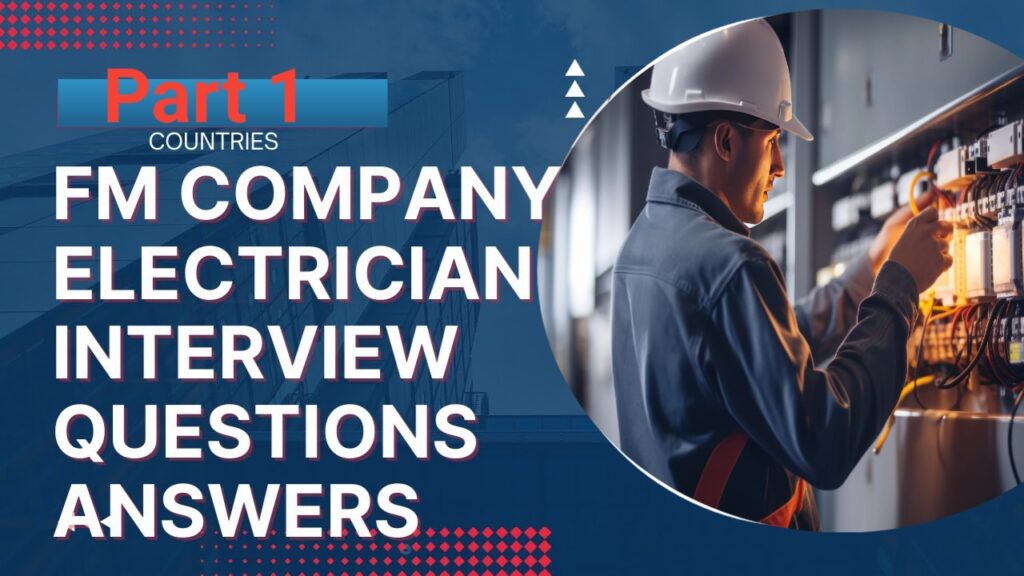
The Ultimate Guide to Electrical Technician Interview Questions for FM Companies
- Answer: Three-phase power uses three alternating currents that are offset by 120 degrees. This setup allows for a continuous transfer of power, as at least one phase is always in the peak voltage stage. In comparison to single-phase systems, three-phase power provides smoother power delivery, is more efficient for heavy machinery, and reduces the load on electrical systems. This is especially important in facilities management where we often work with large motors and HVAC systems that require a stable power supply.
Question 2: How do you approach troubleshooting electrical equipment?
- Explanation: Troubleshooting is a critical skill for electrical technicians. It requires a systematic approach to identify, diagnose, and resolve electrical problems efficiently.
- How to Answer: Outline your troubleshooting process, including the tools you use, safety precautions, and how you identify the root cause of the issue. Mention specific examples from your past experience where your troubleshooting skills were put to the test.
- Answer: When troubleshooting electrical equipment, I start by ensuring that the system is safe to work on by isolating the power source. I then use a multimeter to check for any such as short circuits or open circuits. My process involves checking the simplest possible causes first, such as blown fuses or tripped breakers, before moving on to more complex issues like wiring problems or faulty components. For example, at my previous job, I successfully diagnosed a malfunctioning motor by following this step-by-step troubleshooting process.
Question 3: What safety procedures do you follow when working with high-voltage equipment?
- Explanation: Safety is paramount in electrical work, especially when dealing with high-voltage systems. Employers need to know that you prioritize safety to protect yourself, your colleagues, and the facility.
- How to Answer: Highlight the safety protocols you follow when working with high-voltage systems, including personal protective equipment (PPE), lockout/tagout procedures, and following regulations like the National Electrical Code (NEC) or local standards.
- Answer: Safety is my top priority when working with high-voltage equipment. I always ensure that the power is fully isolated and locked out before starting any work. I use the proper PPE, such as insulated gloves, hard hats, and safety goggles, and double-check that all tools and testing equipment are rated for the voltage levels I’m working with. Additionally, I strictly follow OSHA and NEC guidelines to ensure that all work is compliant with safety standards.
3. Behavioral and Situational Interview Questions
Question 4: Describe a time when you had to work under pressure to complete an urgent repair. How did you handle it?
- Explanation: Facilities management often requires technicians to respond to emergencies, such as power outages or equipment failures. Employers want to know that you can perform well under pressure.
- How to Answer: Use the STAR (Situation, Task, Action, Result) method to structure your response. Describe a specific instance, explain the task at hand, outline the actions you took, and conclude with the outcome.
- Answer: In my previous role, I was called to a factory where a critical piece of machinery had stopped working, causing a production halt. The situation was urgent as every minute of downtime was costing the company money. I quickly assessed the situation, identified that a motor had overheated, and replaced the faulty component. To prevent future issues, I also installed additional cooling mechanisms. The machinery was up and running within a couple of hours, and the client was impressed with the quick turnaround.
Question 5: How do you prioritize tasks when you have multiple maintenance requests?
- Explanation: In a facilities management setting, you might be juggling multiple tasks simultaneously. Employers want to see that you can prioritize effectively to keep the facility running smoothly.How to Answer: Discuss how you assess the urgency of each task, considering factors like safety, the impact on operations, and deadlines. Mention any systems or tools you use to stay organized, such as a computerized maintenance management system (CMMS).
- Example Answer: When managing multiple maintenance requests, I prioritize tasks based on their urgency and impact on the facility’s operations. Safety-related issues always come first, followed by tasks that could cause significant downtime or financial losses if not addressed promptly. I use a CMMS to track and organize work orders, which helps me stay on top of deadlines and ensure that no task is overlooked.
Question 6: Tell us about a time you disagreed with a colleague or supervisor. How did you resolve it?
- Explanation: Interpersonal conflicts are inevitable in any workplace. Employers want to know that you can handle disagreements professionally and maintain a positive working relationship.
- How to Answer: Focus on your ability to communicate effectively, listen to others, and find common ground. Emphasize a situation where the resolution led to a positive outcome for the team or the company.
- Answer: There was a situation where I disagreed with a supervisor about the best way to approach a complex wiring installation. While the supervisor preferred a more traditional method, I suggested a newer, more efficient technique that I had used successfully in the past. We discussed our perspectives, and I provided detailed information and examples of how my approach could save time and reduce costs. After considering my input, we decided to test my method on a small section, and it worked well. In the end, we implemented my approach, which led to a faster project completion.”
4. Industry-Specific Interview Questions
Question 7: How do you ensure compliance with local electrical codes and regulations?
- Explanation: Electrical technicians must adhere to strict codes and regulations to ensure safety and compliance. Employers want to know that you are knowledgeable about these standards.
- How to Answer: Discuss your familiarity with national and local codes, such as the NEC in the U.S., and explain how you stay updated on regulatory changes. Highlight any certifications or training you have completed in this area.
- Answer: I am well-versed in the NEC and local electrical codes. I ensure compliance by regularly reviewing updates to these regulations and attending relevant training sessions. Additionally, I always double-check that my work meets or exceeds code requirements before signing off on any project. For example, during a recent renovation project, I ensured that all new installations were compliant with the latest code revisions, which helped the project pass inspection smoothly.
Question 8: What experience do you have with energy-efficient systems and sustainability practices?
- Explanation: FM companies often focus on sustainability and reducing energy consumption. Technicians who are knowledgeable about energy-efficient systems are highly valued.How to Answer: Highlight any experience you have with energy-efficient systems, such as LED lighting, solar panels, or energy management systems (EMS). Mention any projects where you helped reduce energy consumption or improve sustainability.
- Example Answer: I have extensive experience working with energy-efficient systems, including installing LED lighting and energy-saving HVAC systems. At my last job, I was part of a team that implemented an energy management system in a large commercial building, which helped reduce the facility’s energy consumption by 20%. I am also knowledgeable about renewable energy technologies, such as solar power, and I always look for opportunities to improve a facility’s energy efficiency.
Question 9: What is your experience with building automation systems (BAS)?
- Explanation: Many modern facilities use building automation systems to control various aspects of the building’s operations, including lighting, HVAC, and security. Electrical technicians often play a role in maintaining and troubleshooting these systems.
- How to Answer: Discuss your experience working with BAS, including any specific systems or software you’ve used. Highlight your ability to integrate electrical systems with automation technologies.
- Answer : I have worked extensively with building automation systems (BAS), including both installation and maintenance. For example, in my previous role, I helped install a BAS that controlled HVAC, lighting, and security systems in a large office complex. I worked closely with the BAS technicians to ensure that all electrical components were properly integrated and functioning as intended. This system allowed for more precise control over the building’s energy consumption, resulting in significant cost savings for the client. I’m also proficient with troubleshooting BAS issues, particularly when they involve electrical components.
Question 10: How do you handle working with outdated electrical systems in older facilities?
- Explanation: In facilities management, you may often deal with older buildings that have outdated electrical systems. Employers want to know that you can work effectively with these older systems while ensuring compliance with modern safety standards.
- How to Answer: Discuss your experience with maintaining, troubleshooting, and upgrading outdated electrical systems. Highlight your ability to evaluate whether an older system needs repair or complete replacement. Mention any specific challenges you’ve encountered, such as working with obsolete parts or integrating new technology into an old system.
- Answer: I have extensive experience working with outdated electrical systems, particularly in older commercial and industrial facilities. I always start by carefully assessing the condition of the system and identifying any safety hazards or areas that need upgrading to meet current standards. For instance, in an old manufacturing plant, I upgraded the wiring and replaced outdated circuit breakers with modern ones that provided better protection against overloads and short circuits. I also collaborated with the client to phase in new technology without disrupting their operations.
5. Soft Skills and Teamwork Interview Questions
Question 11: How do you communicate technical information to non-technical stakeholders?
- Explanation: Communication is key in facilities management, where you may need to explain technical issues or solutions to clients, managers, or colleagues who don’t have an electrical background.
- How to Answer: Explain how you tailor your communication style to your audience. Emphasize your ability to break down complex technical concepts into clear and concise language that non-technical individuals can understand. Mention any specific instances where your communication skills helped solve a problem or facilitate decision-making.
- Answer: When communicating with non-technical stakeholders, I focus on simplifying the technical jargon and explaining things in a way that’s easy to understand. For example, if I’m explaining an electrical fault, I might describe it as a ‘disruption in the flow of electricity,’ rather than diving into complex terminology. In one case, I had to explain to a building manager why it was necessary to replace an old electrical panel, and I used analogies like comparing the panel to a car’s engine that was no longer able to handle the demands of modern driving. This helped the manager make an informed decision.
Question 12: How do you manage your time when working on long-term projects with multiple deadlines?
- Explanation: Time management is crucial in FM companies, especially when balancing routine maintenance tasks with larger, long-term projects. Employers want to see that you can prioritize tasks and meet deadlines.
- How to Answer: Discuss your approach to time management, including how you plan and schedule tasks. Mention any tools or strategies you use to keep track of deadlines and ensure that long-term projects stay on track. Highlight your ability to remain flexible and adapt to changes in priorities.
- Answer: When managing long-term projects, I like to break down the project into smaller, manageable tasks and set milestones for each phase. I use project management tools to keep track of deadlines and prioritize my daily tasks accordingly. I also stay in regular communication with other team members to ensure that we’re all aligned and that any potential delays are identified early. For instance, during a large electrical system upgrade for a shopping mall, I had to balance routine maintenance with project tasks, and I managed to complete the upgrade on time without any disruptions to daily operations.”
Nice information and blog…